Supply Chain Challenge
Wynsors Shoes has established itself as a prominent player in the footwear retail industry, known for offering a wide range of styles and sizes to meet varying customer preferences. Operating both e-commerce and brick-and-mortar stores, the company handles a complex supply chain that demands precise inventory management. To streamline these operations, Wynsors Shoes transitioned from a legacy system to AGR in 2017.
ERP integration
AGR integrated with Wynsors new ERP without an issue.
Dependable solution
AGR’s system and people do what they promise.
AGR's people
AGR was professional and approachable from first contact to final implementation. The ongoing support has been really good.
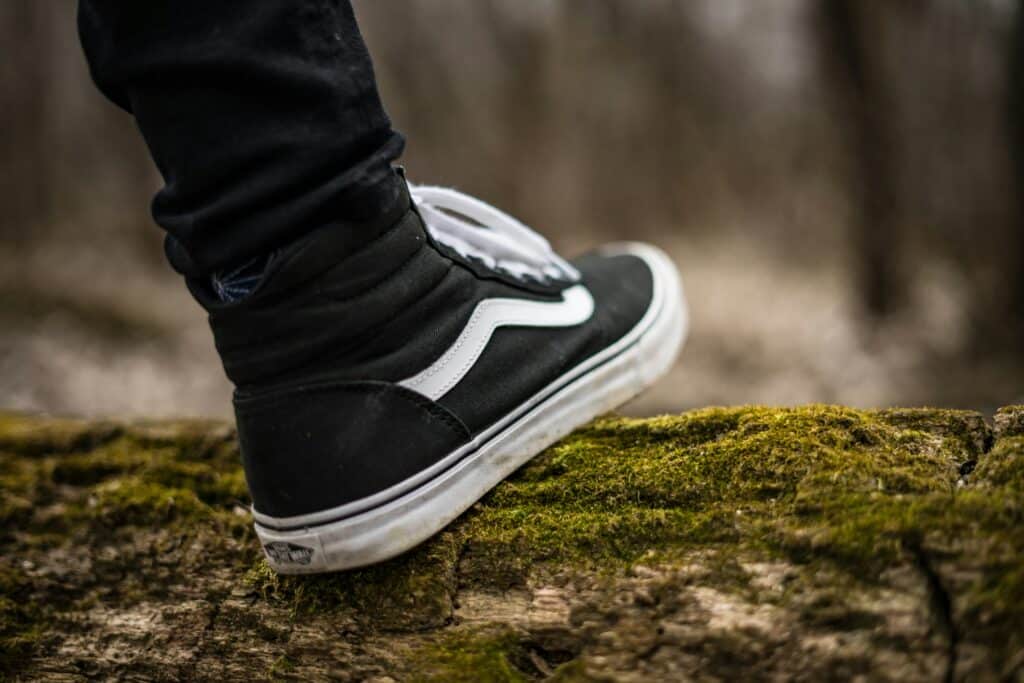
The results
Since implementing AGR, Wynsors shoes has experienced several benefits:
- Operational efficiency
AGR has streamlined replenishment processes, running overnight calculations that save time and reduce manual intervention.
- Improved inventory management
The system’s algorithms optimize the distribution of sizes and styles, ensuring that the right stock is in the right place at the right time.
- Better responsiveness
AGR’s ability to adapt to Wynsors shoes’ unique requirements, such as managing pre-packs and bulk orders, has enhanced inventory accuracy and reduced stockouts.
- Support and flexibility
AGR’s support team has been responsive and helpful, addressing any issues promptly and effectively.
- Wynsors
- Nick Green, Stock Control/E-commerce Manager
Supply Chain Challenge
The supply chain at Wynsors shoes revolves around a central warehouse that handles all stock, both for physical stores and online orders. Weekly deliveries are made to stores using the company’s own transport system. The primary challenges in their supply chain include:
- Inventory Optimization: Managing stock levels for different sizes and styles across multiple locations is complex.
- Long lead times: Managing stock levels for different sizes and styles across multiple locations is complex.
- Global supply chain disruptions: Delays in container deliveries and other logistical issues can affect inventory availability and costs.
The complexity increased with the need to balance inventory across multiple channels, including retail stores, e-commerce platforms, and B2B operations. The lack of a streamlined system often resulted in inefficiencies, impacting customer satisfaction and operational costs.
Need for AGR
Wynsors shoes selected AGR for several reasons:
- Integration capability: AGR’s ability to integrate with their new ERP system was a key factor.
- Functionality and reliability: AGR demonstrated that it could effectively manage replenishment and forecasting needs.
- Positive vendor Interaction: The professionalism and expertise of AGR’s team, particularly during initial discussions and demonstrations, reassured Wynsors shoes of their decision.